Beginning nearly 45 years ago, Amarillo brought to the market what has become the standard for right-angle gearboxes for cooling applications, the Amarillo model 1712. We have taken this popular model and improved and upgraded it further.
The improvements will provide a leak-free design, lower operating temperatures, extended oil life, low-noise operation, lower maintenance, lower cost of ownership, and superior reliability. All brought to you by the Amarillo Gear Company who has been designing gearboxes for over 100 years with world-class manufacturing in the U.S.A.
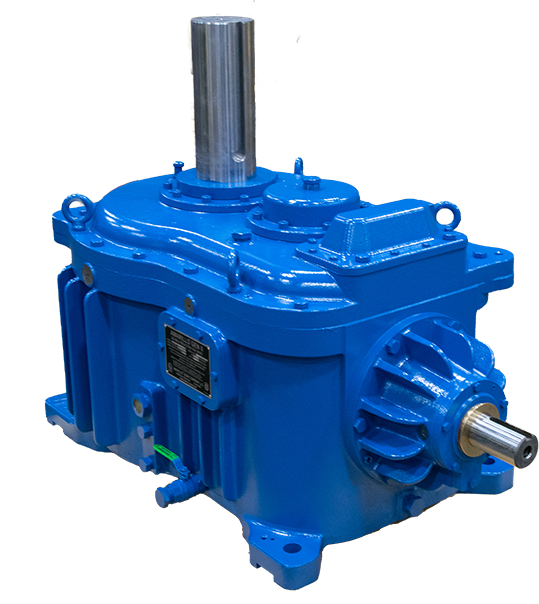
Features
- Leak-free design
- Lower operating temperatures
- Extended oil life
- Low-noise operation
- Lower maintenance
- Lower cost of ownership
- Superior reliability
- Drop in replacement for Amarillo 1712
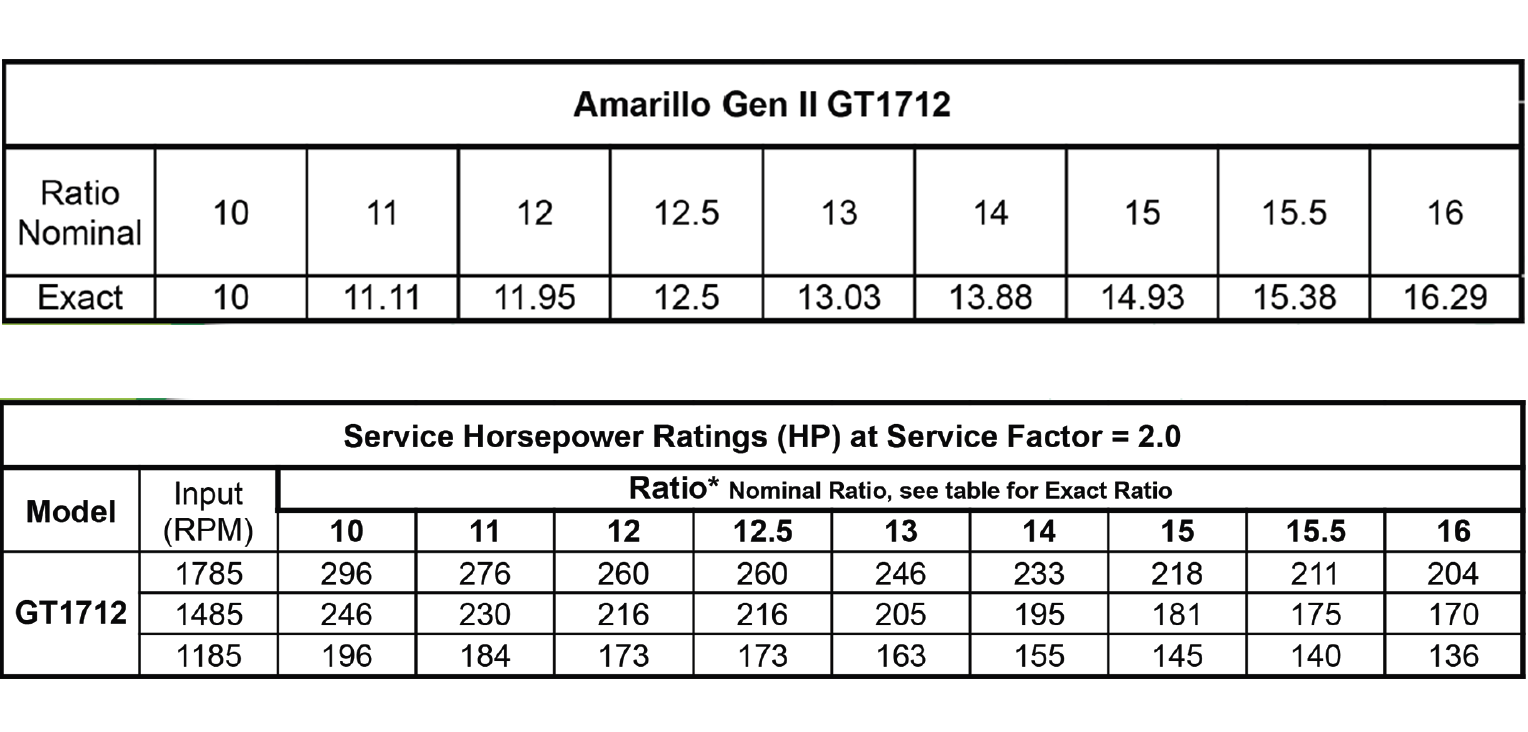
Details
Gearboxes shall be of design specific to their application for superior reliability. Gearbox manufacturers shall have ISO 9001:2015 quality certification, or the most current.
The purpose of the gearbox is to reliably drive and support a large axial fan in a cooling application over its design life. It is a reducing design, reducing the speed of the fan to the required torque and speed. It must be able to withstand momentary shock loads at start-up. The output shaft shall act as a stable spindle for the large axial fan to attach to. It shall operate with greater than 95% efficiency and quietly during its life with minimum maintenance required.
Each gearbox shall feature a double reduction design, incorporating a helical gear and a spiral bevel gear stage. Design standards used shall be to AGMA STD 6013- B16 (or most current) and shall additionally meet or exceed the requirements of CTI (Cooling Technology Institute) STD 111. Selection of the gearbox shall be with a service factor of not less than 2.0 based on motor nameplate rating. Thermal rating of the gearbox shall be equal to or exceed the nameplate rating on the gearbox without auxiliary cooling.
The gear case shall be of specific design for the application. It shall be able to withstand all operational loads within its selection criteria. It shall be designed to maintain gear and bearing alignment throughout its operational life. Maximized spacing between upper and lower bearings is also key to a stable output shaft spindle. The gear case shall include raised lower bearing housings with a sloped floor to facilitate the removal of contaminants and lubricant from the gear case during an oil change. Gear case design shall allow for improved noise attenuation. Casting materials shall be not less than ASTM A48 Class 30 gray iron and include cooling fins on the body and horizontal carrier to maximize thermal capacity.
All bearings shall be of tapered roller design with tier 1 quality. All bearings shall achieve a rating of not less than 100,000-hour L10a life when operated at maximum nameplate ratings. All bearings shall be of metric sizing to ensure ready availability in the event bearing replacement is required. Thrust bearings shall be sized such that larger bearings are selected in lieu of multiple “stacked” bearings.
All bearings and gearing shall be splash-lubricated by means of an internal oil slinger attached to the input shaft. Gearbox shall be able to reliably lubricate at input speeds down to 400 rpm, moving lubricant through optimally designed oil channels. Operation under load at speeds less than 400 rpm is permitted with the addition of an optional mechanical oil pump. Gearbox shall be able to lubricate in CW or CCW rotation unless the gearbox is outfitted with a non-reverse backstop option.
All gearing shall be of proven design. Gearbox shall be provided with in-house generated and finished gearing to ensure gearbox manufacturer follows and is in control of all quality processes. Gear material shall be AISI 8620 or AISI 4320 alloy steel and be case-carburized for optimum strength and long life. Carburizing operations shall be controlled by the gearbox manufacturer to provide proper microstructure and case depth with a surface hardness of 58 – 64 HRC. Spiral bevel gearing shall maintain AGMA class Q9 or better. Gearing may be either ground or lapped to ensure smooth and quiet operation. The spiral bevel pinion gear shall be integral to the input shaft in lieu of a separate hub pinion/input shaft design. Helical gearing shall be AGMA class Q10 quality or better.
A removable inspection plate shall be provided. Sealing of the gearbox, while allowing the gearbox to properly breathe, is of optimum importance. Gearbox sealing design shall be such to minimize oil contamination while preventing oil leaks. The input shaft shall be sealed using a non-contact bearing isolator that will not wear over time. The output shaft shall be sealed with a labyrinth design. Use of wear seals are not allowed.
Assembly of the gearbox shall use spacers and shims to set the gears and bearings. Every gearbox shall be tested after assembly to ensure proper operation. Full load testing in the gear manufacturer’s test lab shall be available if required. After testing, the gearbox may be supplied with the first fill of lubricant to provide protection to the interior surfaces of the gearbox. Optional long-term storage options shall be available that prepare the gearbox for periods of extended storage.
Final surface finishing shall be accomplished with epoxy-type coating.